Evans Evco Converting & Fabricating Capabilities
How do we choose a fabrication method for your custom converted product?
Controlling cost and quality gets to the heart of how we approach every job, and that guides our decision-making process.
With each new process we adopt, there’s a promise to our customers to leverage it to achieve the best possible value for our customers.
We have decades of experience fabricating adhesives and elastomeric materials. That means we know exactly how a given material will respond to each specific manufacturing process. So our production plan is designed around achieving the best fit and the highest quality the job demands.
We’re also committed to designing each run to minimize material waste through nesting and placement to capture the highest yields from every inch.
Finally, we factor in the fabrication method that best streamlines production time.
To learn how we achieve value and quality, explore our range of capabilities.
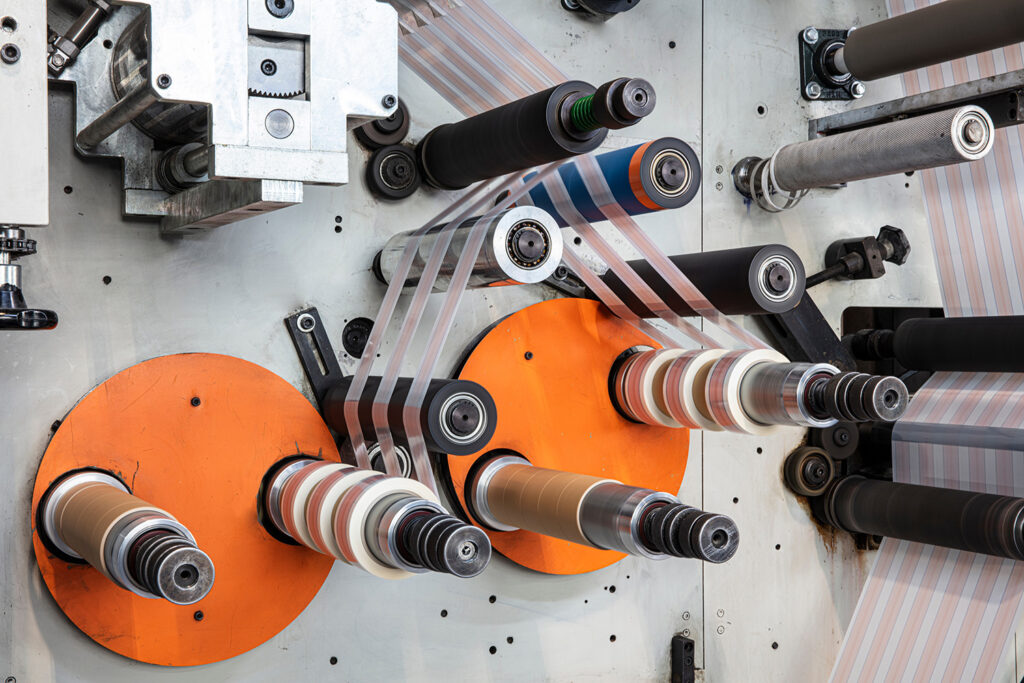
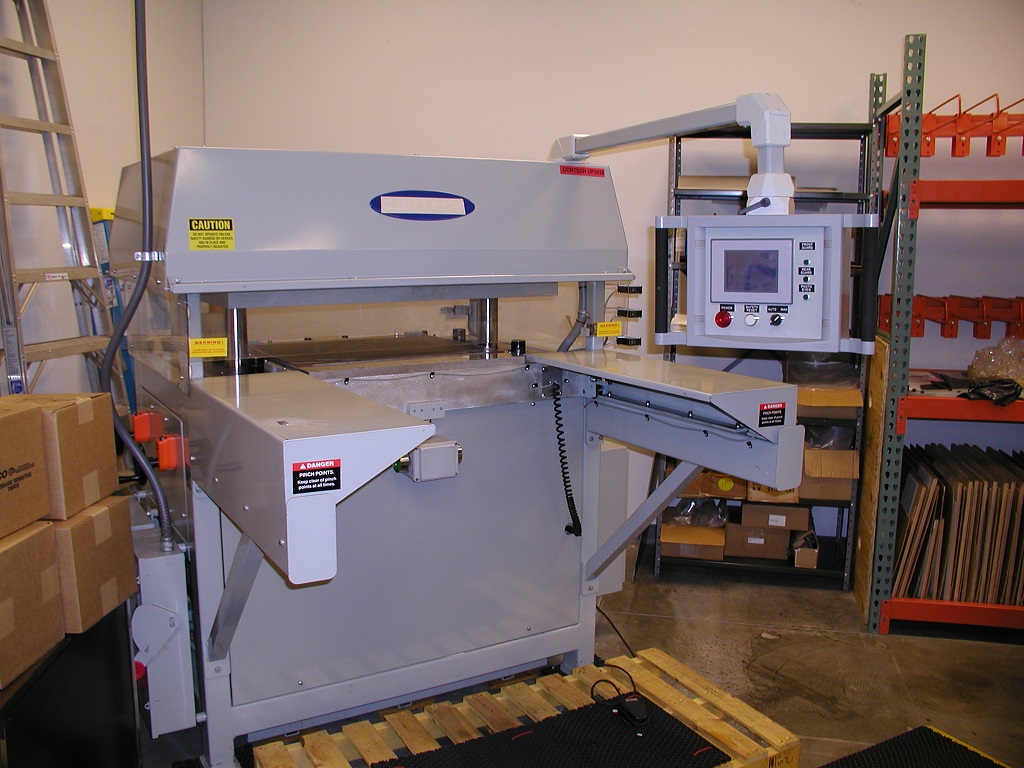
For fabricating gaskets and other custom shapes, flat-bed die cutting offers one of the most cost-effective fabrication methods. The steel rule dies are often less expensive than custom rotary dies. Because this method enables us to group and nest the cut shapes, this method is optimal for keeping material waste to a minimum. For smaller-volume jobs, flat bed’s rapid changeover process makes it an efficient method.
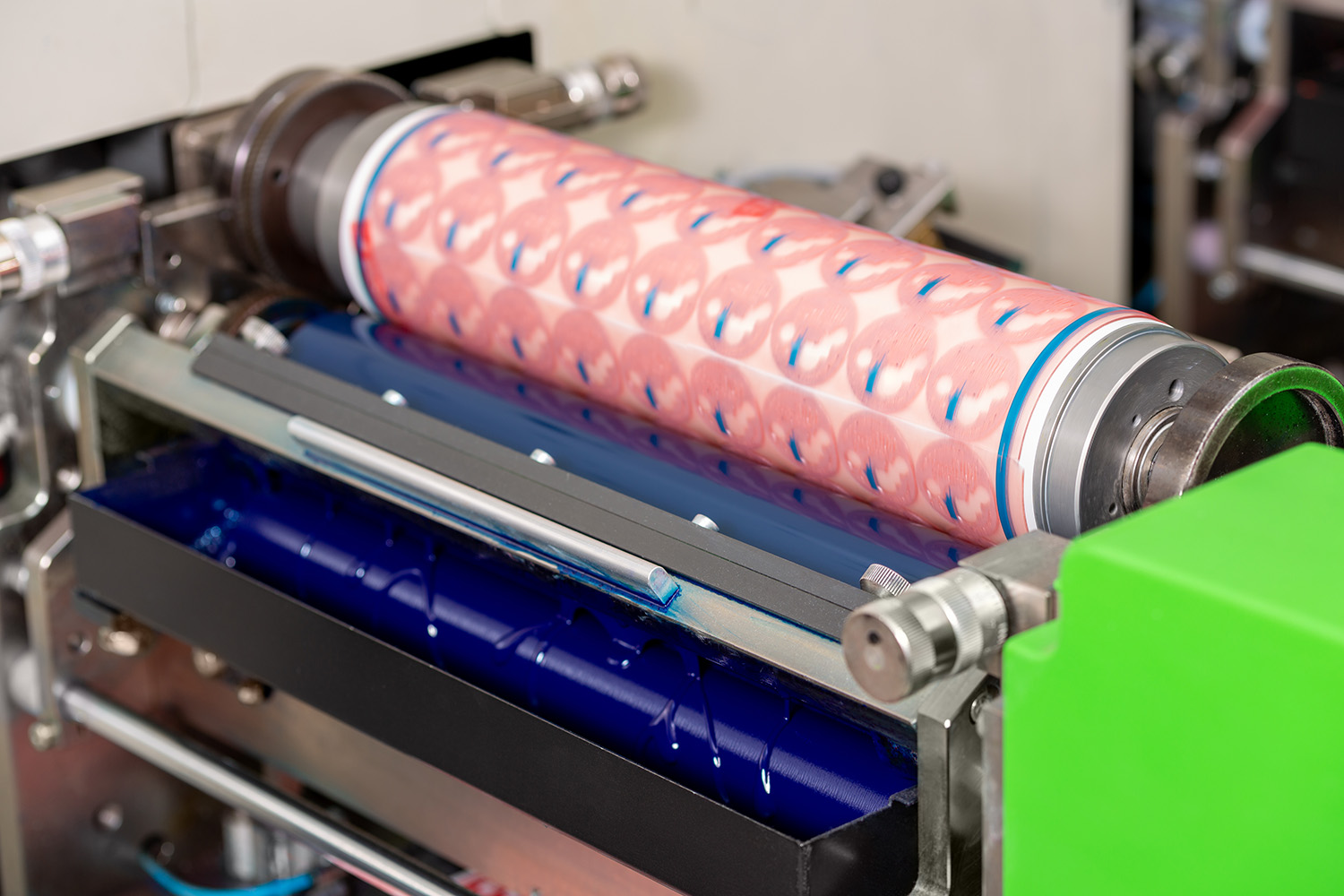
We offer rotary die cutting as a versatile and precise method for fulfilling large volumes of custom shape parts, particularly from thicker material. As the cylindrical die cuts shapes from soft materials, the vertical die cut maintains exceptional tension control to consistently produce uniform shapes, making it a cost-effective fabrication method for jobs requiring tight tolerances. The ability to control the depth of the cut makes this an efficient method for achieving kiss-cuts, extended liners, linear perforating, cross perforating and scoring for ease of assembly.
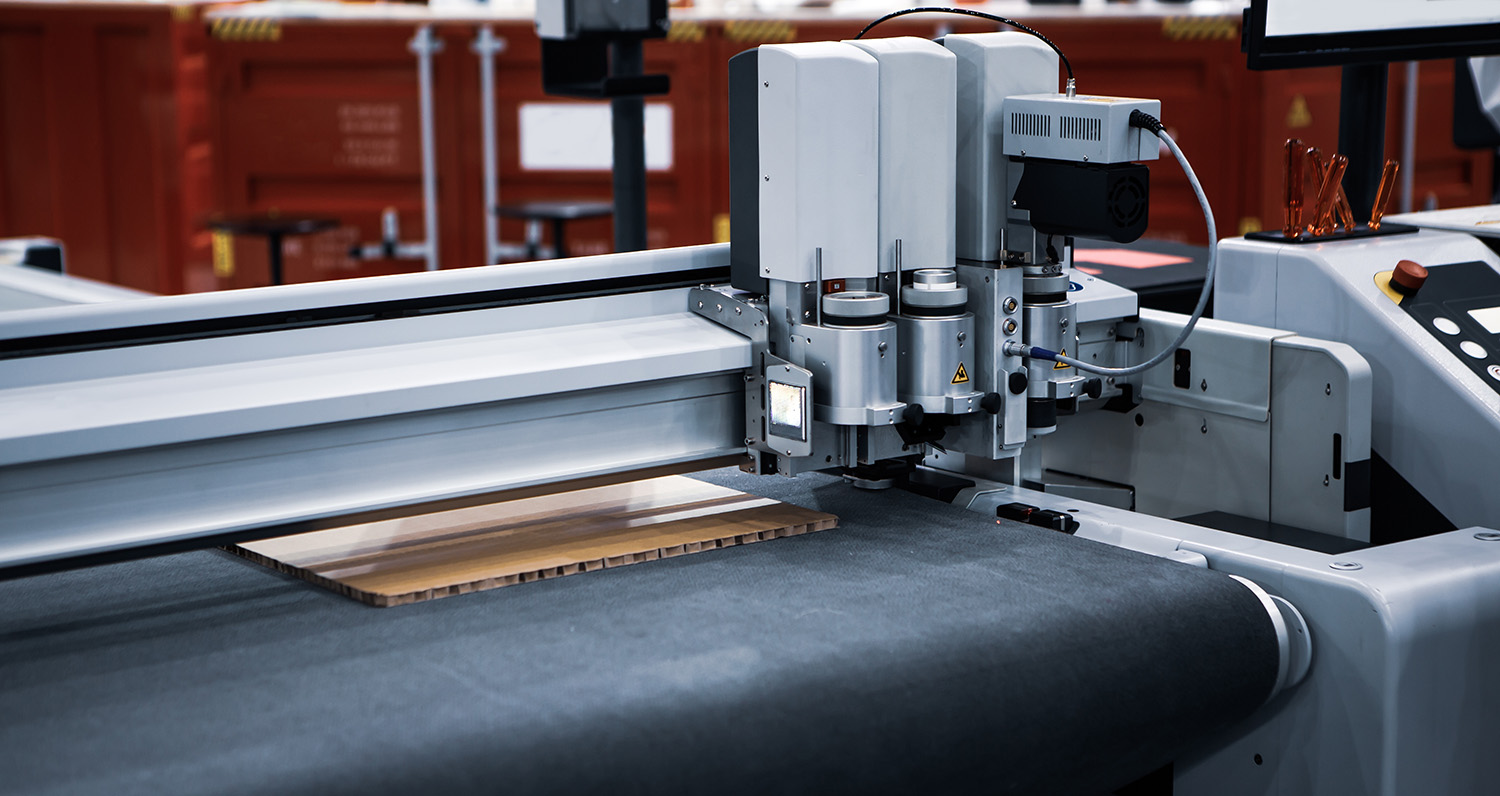
No expensive metal dies are needed here, which makes digital cutting ideally suited for small volume projects, short timelines and prototyping. Once we upload the final design into the operating system, production can begin. The software controlled operating system keeps material waste to a minimum through its nesting capabilities, while achieving the most intricate cuts with exceptional precision.
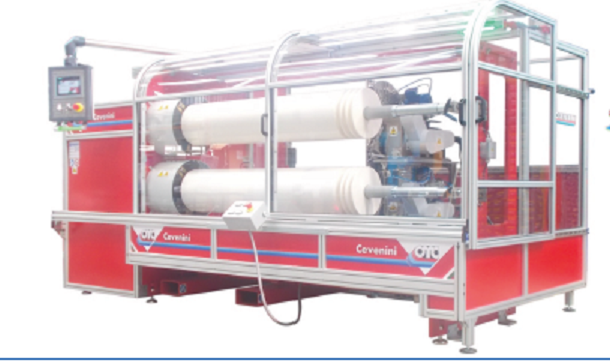
We cut jumbo rolls into your desired width, from 1/16″ to 60.” Sourced from master rolls of tape, foam, liner, adhesive or foil, or produced from custom laminated materials, our single blade cutting services can manufacture rolls tailored for your operation and machinery, from printing to light manufacturing.
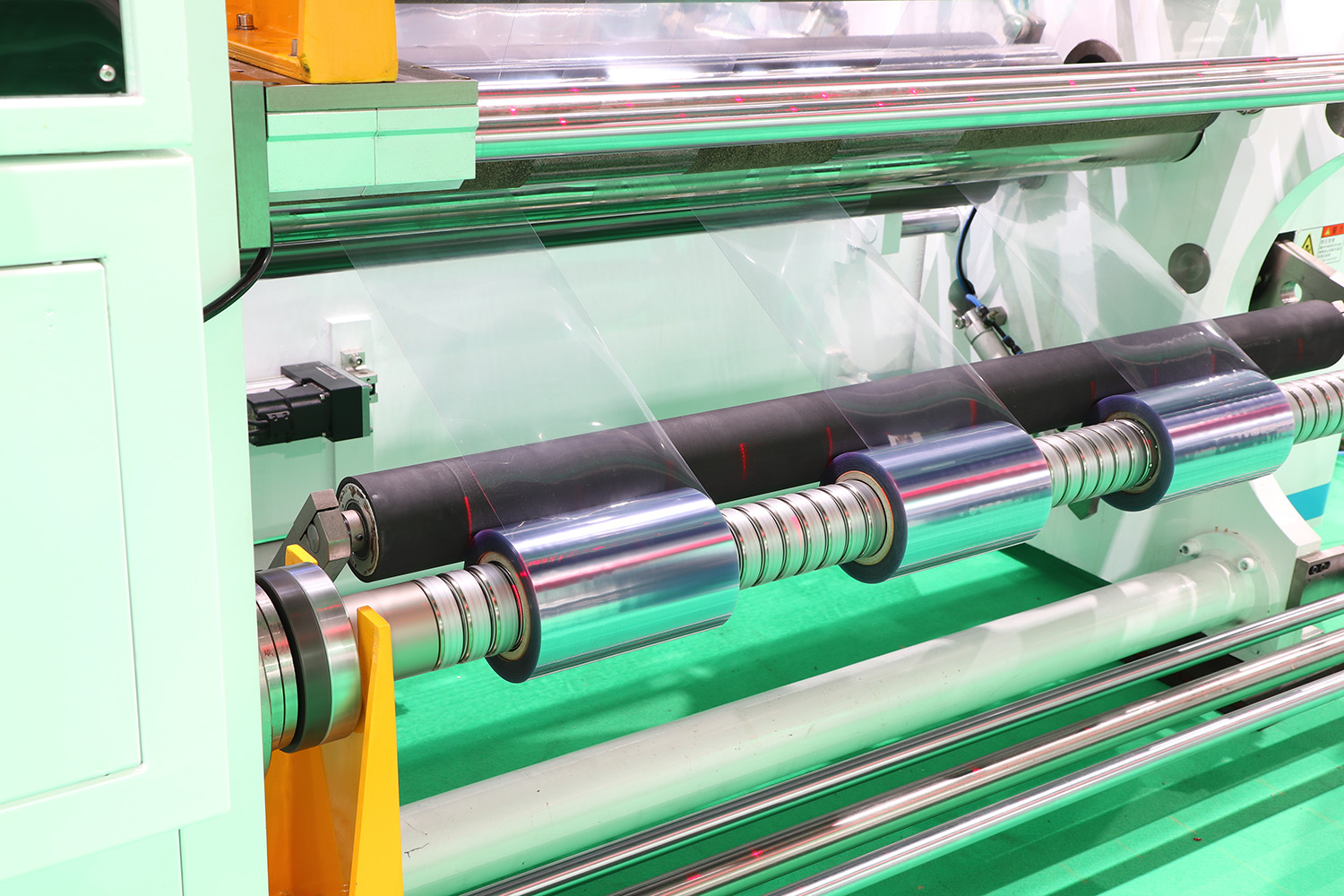
Build a completely customized roll of material sourced from sheets and rolls of tape, film, foil, foam, adhesive and liner. You can rely on our expertise to identify the slitting method — score, shear or razor cutting — for your chosen material that achieves the highest quality results. We produce uniform strips at widths ranging from 1/2″ to 60”, with the option to splice before rewinding the material onto 1.0”, 1.5” or 3.0-inch cores.
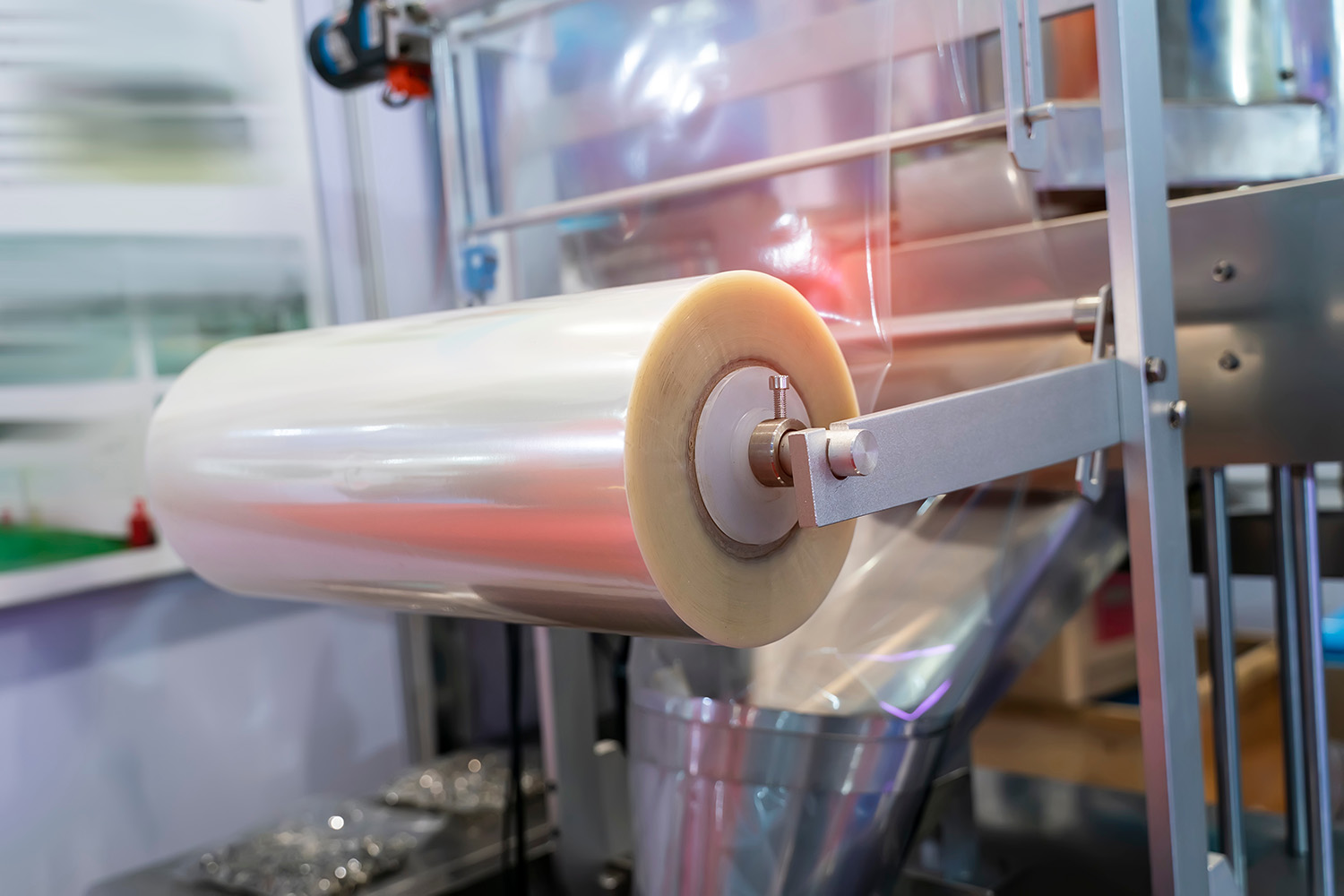
Finishing errors and improper storage can result in misshapen rolls of tape, which can disrupt production because of their inability to unwind smoothly on a manufacturing machine. With our salvage rewinding services, we can evaluate the efficacy of damaged tape rolls, and apply salvage rewinding to restore them to like-new — all for a fraction of the cost to discard and replace. We work on rolls at a maximum of 2.5-inch rolls at a maximum diameter of 12.0 inches.
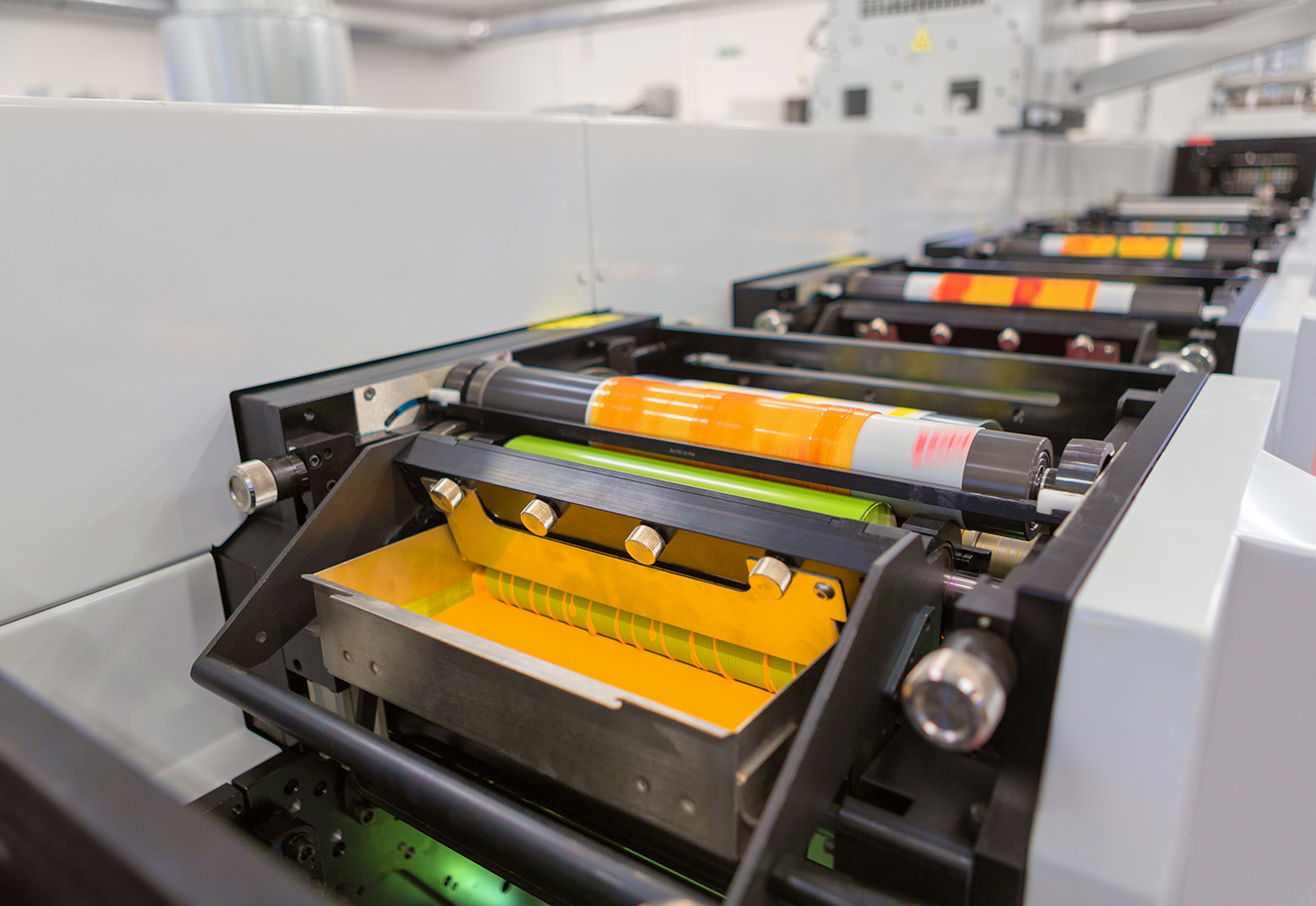
Send the right message by tapping our expertise to produce custom printed tape, with applications ranging from tamper proof labeling, package instructions, product labeling and so much more. Our flexographic printing process achieves clearly rendered text on just about any tape carrier—permanently. Flexographic printing offers additional value as the finished job needs no special coatings to seal and protect the integrity of the message. Through our process, you can achieve consistent messaging that always comes through even after the hazards of shipping, storage, weather and more.
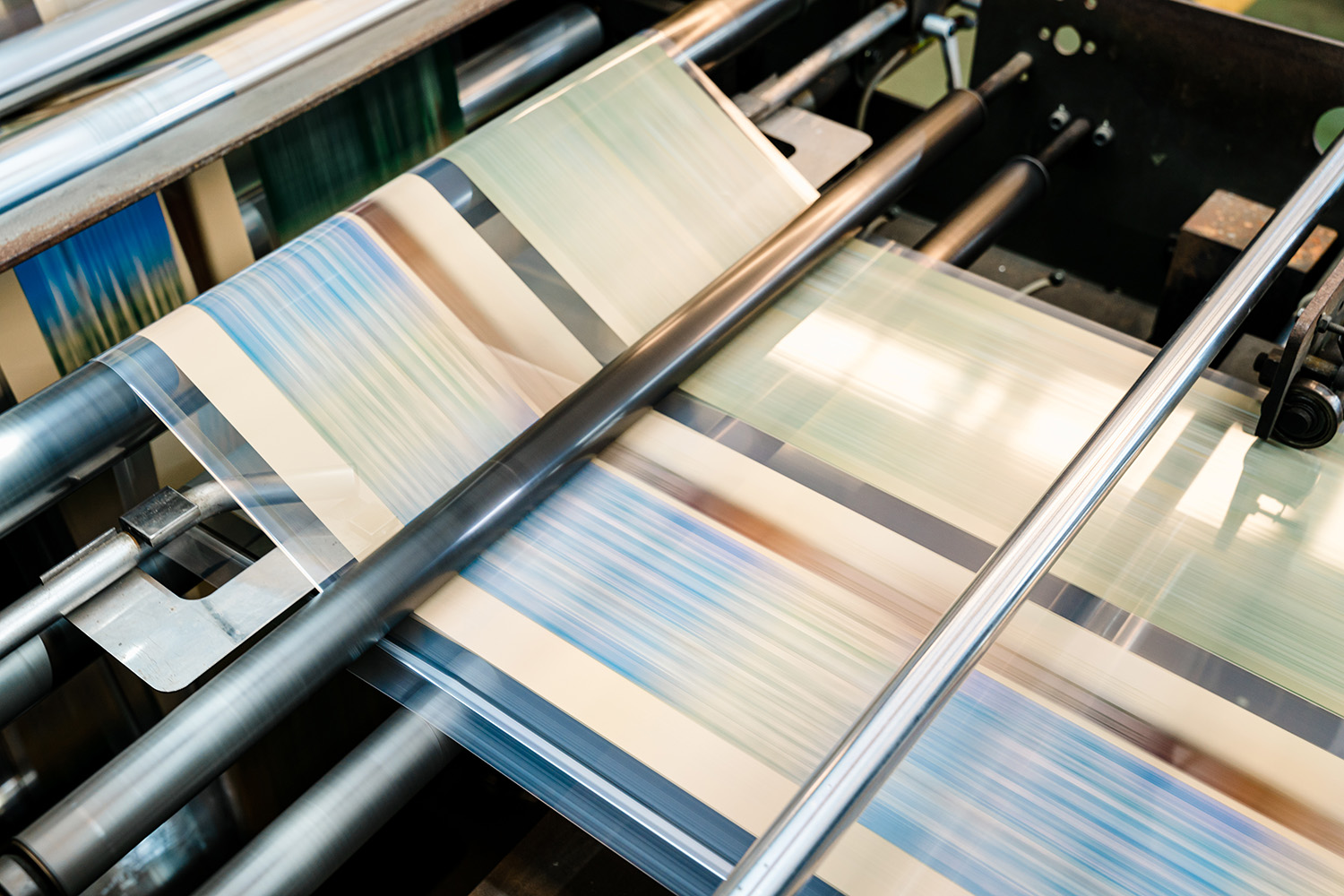
Rely on our technical acumen when it comes to selecting the best foam, pressure-sensitive adhesives, films, foils and other materials for laminating into one customized product for your unique application. With our product knowledge, we understand how the materials will perform as a unit and which lamination process will result at the best quality at the best value. We offer cold laminating, heated laminating, single-layer laminating and multi-layer laminating to ensure success.
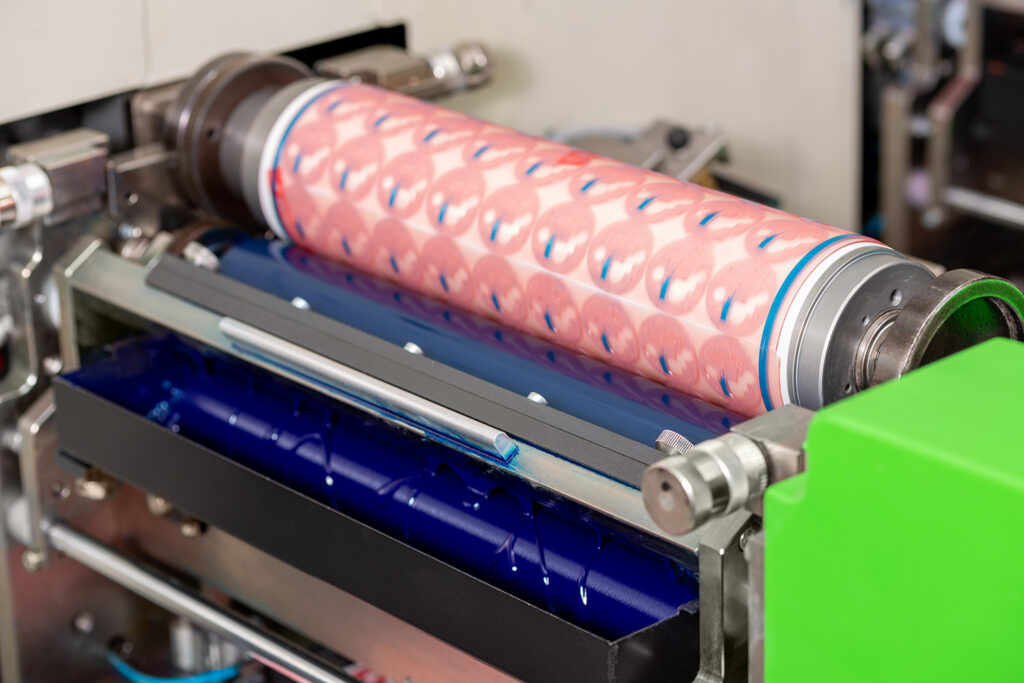
At Evans Evco, we pride ourselves on our core capabilities in fabrication and manufacturing. With our decades of experience and our focus on cost control and quality, we select the most suitable fabrication method for each custom converted product. Our deep product knowledge on pressure sensitive adhesives and elastomeric materials allows us to optimize production plans, minimize material waste and streamline production time.
Whether the best fabrication method calls for die cutting, slitting and rewinding or custom lamination, we have the knowledge and tools to deliver exceptional results.